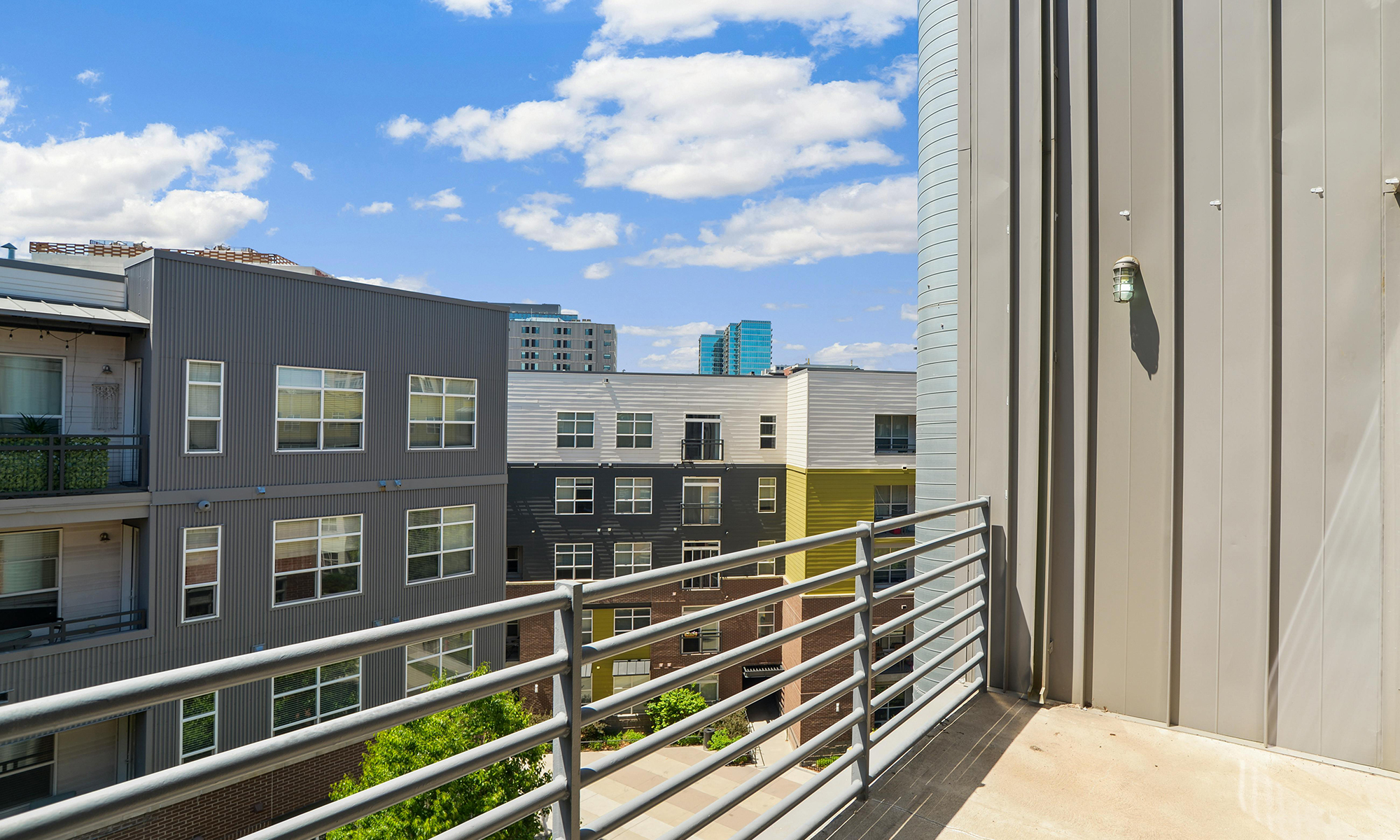
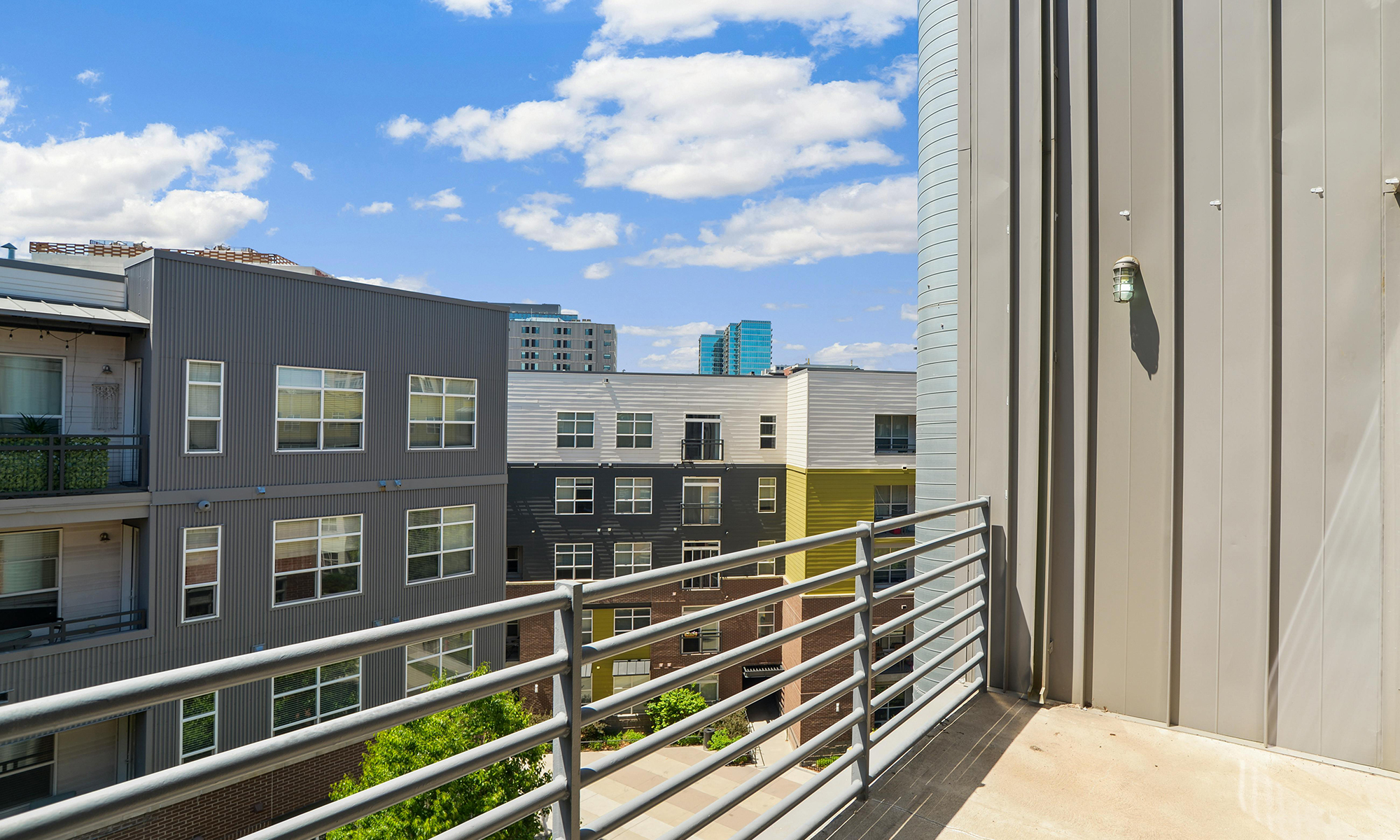
Blog
Third-party commissioning increases the likelihood that a PV system will perform as designed throughout its lifetime and reduces poorly performing PV systems, which erode the bottom line and damage solar energy’s reputation.
Falling costs and rising demand for clean energy have increased the specification and installation of solar photovoltaic (PV) systems worldwide. In NYC, Local Laws 92 and 94 require solar PV and/or green roofs on all new buildings and alterations where the existing roof deck is being replaced. Third-party commissioning increases the likelihood that a PV system will perform as designed throughout its lifetime and reduces poorly performing PV systems, which erode the bottom line and damage solar energy’s reputation. This is probably why the NYC Energy Conservation Code requires that renewable energy systems greater than 25 kW be commissioned (C408.2).
Many factors can affect a PV system’s power output. Let’s look at some reasons why output may be less than expected.
Commissioning agents help prevent design flaws when brought onto the project early in the process. Here are a few common design flaws:
Electrical Issues: In traditional string systems, modules are wired in series to increase voltage, as shown. However, if too few or too many modules are wired in series, the voltage will be outside of an inverter’s input range and there will simply be no power output. If modules of dissimilar current are wired together output will be reduced since the current of a string is limited by the module with the lowest current.
Shading Losses: Not only does shading reduce output, but a suboptimal tilt and azimuth angle (compass direction) can reduce expected production. A solar pathfinder can help designers find sources of shading and, if possible, remove them. While it may not be feasible to change the tilt and compass direction of the array to point more directly at the sun, a commissioning agent will check the tilt and azimuth angles specified in the design to compare against the as-built so the owner knows what to expect.
System Placement: Another common design issue for ballasted rooftop systems is that mechanical equipment can exhaust combustion air up toward the array, heating it, which decreases voltage and performance. Also, a simple lack of access for maintenance staff to clean the array can severely degrade output over time.
In any discipline as-builts differ from design. It is the job of the commissioning agent to ensure deviations do not diminish performance. These issues can range from a minor reduction in power output to major safety risks.
Wire Management: Wiring in PV systems must be able to withstand weather and extreme temperatures for 20+ years. Any sagging wires, as shown below, can lead to weak connections and frayed insulation over time. A commissioning agent also checks to make sure either PV wire or USE-2 is specified for PV circuits outside of conduit that can withstand temperatures up to 194 F in wet or dry conditions.
Electrical Continuity: A commissioning agent can ensure that all modules are mechanically bonded. For example, in a ballasted system modules must be mechanically bonded to rails using WEEBs (Washer, Electrical Equipment Bonds), as shown below, so all equipment is at the same potential.
Ground Faults: Ground faults have been a longtime concern for PV systems. They occur due to an unintended electrical connection between a conductor and the equipment grounding conductor (EGC), as shown, which carries stray current to ground. This results in a loss of power and a fire hazard where bare metal is heated by the stray current. These types of faults are caused by damaged conductor insulation and pinched wires, all of which are checked during commissioning.
Reversed Polarity: Another dangerous condition is when the modules are accidentally wired in reverse (reversal of the polarity), which can blow the fuse in the combiner box due to high current.
Even when the installation is executed perfectly, manufacturer’s defects may be present. For example, a faulty cell can result in hot spots, the accumulation of current and heat on a short-circuited cell, leading to reduced performance and, in extreme circumstances, fire. Thermal imagers, used in commissioning and retro-commissioning, can quickly identify hot spots.
While inspecting a 2 MW PV array in West Africa, we noticed the energy output was abysmal, less than half of the expected production. Upon visual inspection we saw the modules were covered in a layer of sand, and after speaking with the maintenance staff, realized that no access pathway for cleaning had been accounted for in the design. Now the maintenance team can only wait for the rain, which occurs for only three months out of the year in this desert country. Not only will the modules not be cleaned for nine months, but rainwater may make the situation worse depending on the mineral content and pH – corroding the modules or leading to calcium buildup on the frames. For that reason, we recommend that modules in areas with high mineral content water be washed with deionized water to prevent a film of hard-to-remove mineral deposits.
From optimizing power output to preventing stray current, commissioning a PV system is well worth it, but also requires professionals with deep expertise. To find out how SWA’s Cx Group can help Contact us.
Contributor: Michael Ginsberg, Building Systems Consultant, NABCEP PV Installation Professional
Steven Winter Associates